Article
New Case Packers Optimise Compaxo's Processed Meats Line
In response to growing retail demand for sliced meats, the Dutch based Compaxo decided in 2022 to automate two of its production lines. With limited floor space available in the factory, the company opted for two compact BPA case packers to package thermoformed packs into boxes or crates. Production Manager Jeroen Tuiloo (on the image right) and Technical Service Head Gijs Noorlander (on the image left) reflect on the project.
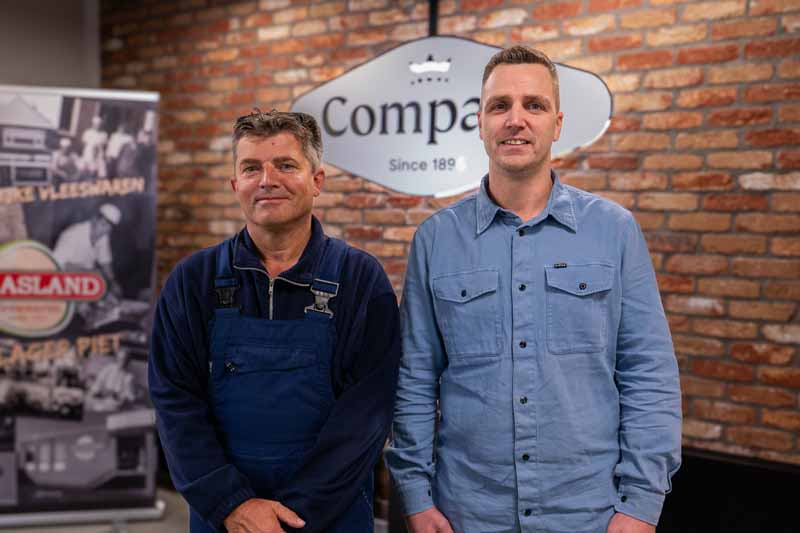
Space-Saving Robotics
The integration of the new case packers presented significant challenges, particularly due to limited floor space in the factory. Installing the machines required precise coordination and collaboration with BPA, Noorlander notes. “BPA was highly cooperative and came up with practical solutions.”
For both lines, BPA installed a Gantry 300 case packer. This two-axis robot is designed to save floor space by operating vertically above the production line. This layout allows Compaxo to maximize its available space without the robot itself occupying much space.
At production line 6, which fills both crates and boxes, thermoformed packs arrive via a dual infeed. The BPA Gantry 300 uses vacuum grippers to pick up two sets of eight packs per lane and places them horizontally into two or four pre-positioned CBL crates or boxes.
Production line 8 is dedicated to packing thermoformed packs into display boxes. Here, a single infeed is sufficient, and the packs are positioned upright in the boxes. The Gantry robot groups and places the packs into an intermediate cassette. During the transfer, the robot’s vacuum grippers rotate the packs so they are oriented correctly in the display boxes. A pusher then moves the packs from the cassette into tilted display boxes, which are subsequently returned to an upright position and transported via an outfeed conveyor to the palletizing station.
Images from Line 8 Process
- The Gantry robot picks packs from the infeed.
- Vacuum grippers rotate packs and place them in the intermediate cassette.
- Filled boxes return to an upright position.
- Filled boxes exit while new boxes are positioned.
- Display boxes show upright packs oriented for readability.
Efficiency, Flexibility, and Cost Savings
“We’re not just buying a machine but a service that must deliver on promises,” says Tuiloo. “In BPA’s case, we are certainly satisfied. The case packers offer great flexibility with programmable packing patterns and the ability to handle various tray and box sizes. This adaptability makes it easy to respond to changing demands and packaging specifications without significant downtime. Changeovers are completed within five minutes. This efficiency has boosted production speed, resulting in a more stable and higher output. Additionally, automating manual tasks with these machines has reduced our labor costs.”
Future-Proof Operations
During the initial start-up phase, the new case packers required adjustments to align with the speed of upstream production processes. Thanks to close collaboration between Compaxo and BPA technicians, these challenges were quickly resolved, says Noorlander, praising BPA’s problem-solving approach.
After several months of operation, the Compaxo team is pleased with the results. “The case packers meet our expectations, achieving the desired production speeds and improving efficiency,” Tuiloo states. Noorlander adds, “While there were always points for improvement, BPA’s service and problem-solving mindset ensured a positive outcome. It’s about how we address issues together, and BPA did an excellent job.”
In conclusion, Tuiloo says, “The investment in new BPA case packers aligns with our growth ambitions and modernization strategy. By further automating our processes, we can meet growing retail demand and remain prepared for future challenges.”